Korozja jest zjawiskiem, w którym materiał ulega reakcji chemicznej lub elektrochemicznej z otaczającym materiałem, co powoduje rozpad. Niezależnie od tego, czy w naszym życiu codziennym, czy w produkcji przemysłowej „rdza” metalu można zobaczyć wszędzie, od małej korozji śruby, dużych samochodów, samolotów, mostów i innej korozji. Korozja nie tylko spowoduje straty ekonomiczne, a nawet doprowadzi do wypadków bezpieczeństwa, ale nie należy lekceważyć znaczenia antykorozji.
W warstwie granicznej podłoża zostanie wygenerowana pierwsza warstwa reakcji. Ze względu na obecność tlenu w atmosferze warstwa reakcyjna zwykle istnieje w postaci tlenku i dlatego jest również znana jako pierwotny film o tlenku (POF). Ta warstwa jest zwykle cienka i początkowo zapobiega dalszej korozji.
Oprócz warstwy reakcji substancje gromadzą się w zaadsorbowanych warstwach. Zwykle pierwszą jest woda, która ze względu na amfoteryczny charakter większości tlenków metali reaguje z pierwotnym filmem tlenku w reakcji kwasowo-zasadowej, tworząc wolne grupy wodorotlenkowe na powierzchni, w których można również osadzić inne substancje reaktywne. Ta warstwa jest warstwą chemisorpcyjną, która jest silnie związana i trudna do ponownego rozolecia. Po warstwie chemisorpcji jest ściśle fizyczna warstwa adsorpcji, która ma słabe wiązanie molekularne i jest łatwo wymieniona.
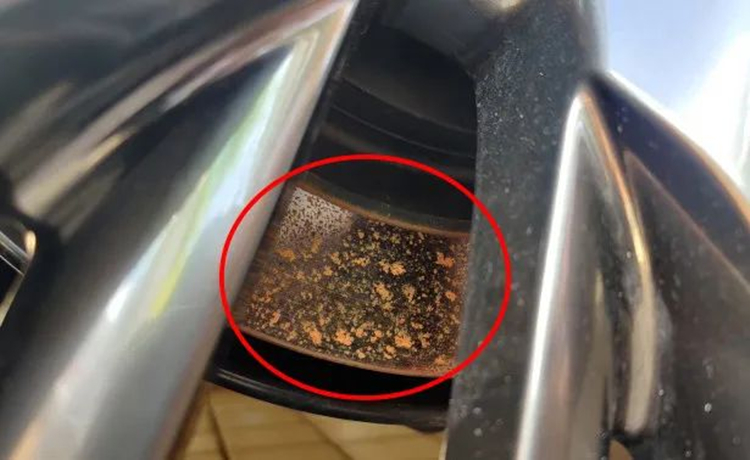
Pierwotna folia tlenku jest najważniejszą warstwą odporności na korozję, tym grubsza film, tym silniejsza przyczepność, tym większy odporność na korozję. Innymi słowy, podczas tworzenia i stabilizacji pierwotnej folii tlenkowej (POF) należy rozpocząć ochronę korozji. W zależności od materiału metalowego wymagane są dodatki (np. Środki powierzchniowo czynne, czynniki redoks). Korozja zwykle zaczyna się od rozkładu pierwotnej folii tlenkowej, która jest wysoce prawdopodobne, że występuje w niezwłocznie stalowych materiałach, ale w stali nierdzewnej pierwotna folia tlenku jest bardziej stabilna ze względu na obecność składników stopowych (zwłaszcza chromu).
Wspólna korozja w życiu ma wiele różnych form ekspresji, spójrzmy na następujące siedem ważnych rodzajów korozji.
1. Korozja erozji:Metal poddawany erozji prawie równolegle do powierzchni. Jest to najczęstsza forma korozji i jest zwykle spowodowana wodą lub brudnym powietrzem.
2. Korozja szczelinowa:szczeliny między metaliami lub elementami strukturalnymi mogą prowadzić do ciężkiej korozji, ponieważ elektrolit jest zachowywany przez działanie naczyń włosowatych i mogą powodować duże różnice stężenia. Można to skutecznie zapobiec poprzez środki optymalizacji projektowania.
3. Kontaktowanie się z korozją:Korozja elektrochemiczna wynikająca z kontaktu z dwoma odmiennymi metaliami, jednocześnie w elektrolicie, z jednym z metali z znacznie szybszym prędkością. Można temu zapobiec, wybierając odpowiednie materiały lub przerywając przewodność między materiałami.
4. Pitting:Pitting powoduje wżer, kraterowanie lub wskazanie. Zazwyczaj jest to spowodowane uszkodzeniem warstwy ochronnej, takich jak pory w powleczeniu lub erozji chlorku na warstwie pasywacyjnej.
5. Korozja międzygranowa:Głównie ferrytu Cr i Crni austenitic stal w granicach ziarna są erodowane, korozja ta spowoduje, że wiązanie między ziarnami znacznie się osłabia. Poważna korozja międzykrystaliczna może sprawić, że metal utracono wytrzymałość i ciągliwość, rozpadając się pod normalnym obciążeniem, odpowiednie obróbka cieplna ma zapobiegać korozji międzykrystalicznej przesłanki.
6. Korozja wzrostu:Korozja w punkcie rosy odnosi się do nasyconej pary z powodu chłodzenia i kondensacji do cieczy na materiale spowodowanym korozją, stalą o niskiej płaszczyzną, stalą nierówną, a stal nierdzewna CRNI jest podatna na silną erozję, musi być chroniona przez odpowiednią warstwę ochronną.
7. Pękanie korozji naprężeń:W pożywce żrących, podczas gdy pod naprężeniem mechanicznym materiał będzie tworzy pęknięcia, szczególnie w roztworach chloru i silnych alkalicznych, doprowadzi do stali austenitycznej CRNI w pęknięciu korozji naprężeń.
Czas po: 21-2024